Fully Automatic Grease Plant
Production capacity | 5 to 30* tonnes per day |
Types and grades of grease | Calcium, Lithium, Aluminium Complex Greases |
Base oils required | Both naphthenic and paraffinic |
Package sizes to be filled | Small plastic tubs, cans and 180-200 kg drums |
Shift pattern | 1 x eight hour shift, five days per week |
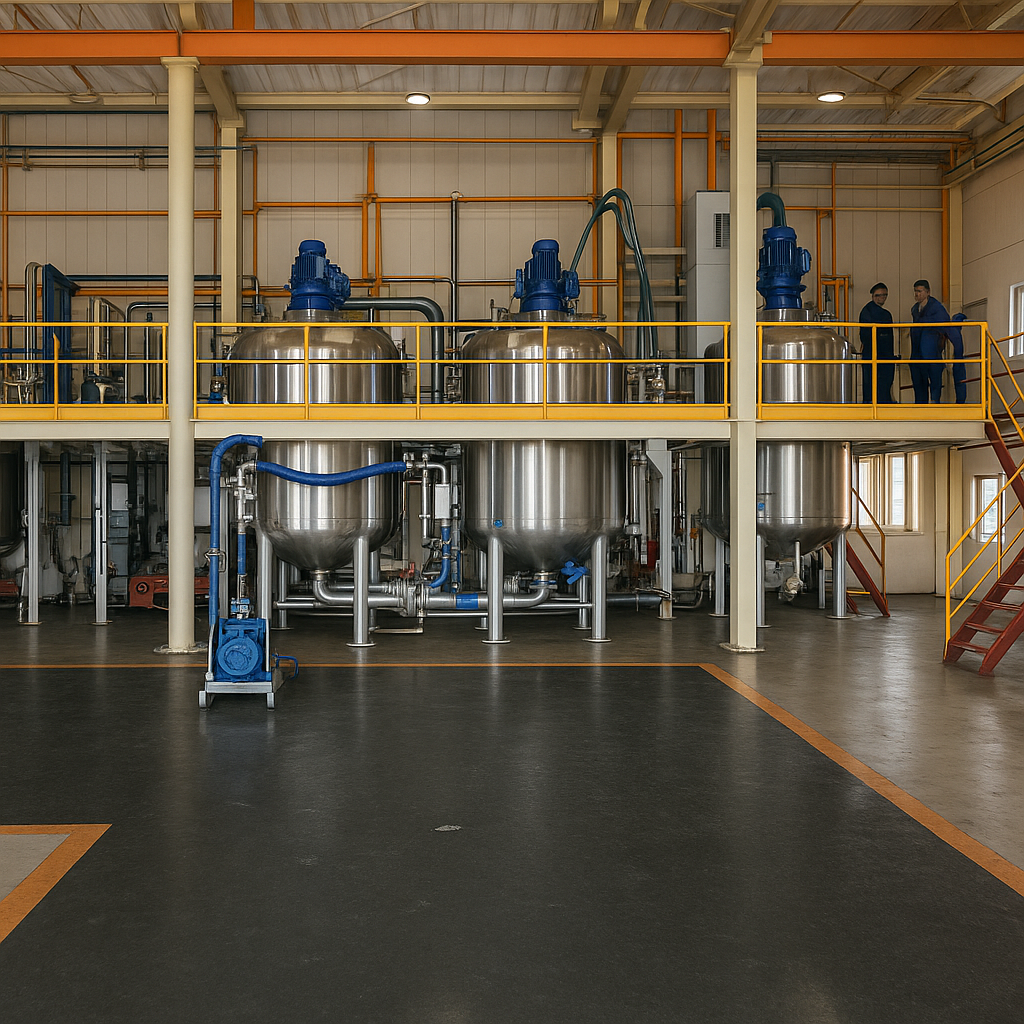
High-Efficiency Pressure Saponification
Our Grease Manufacturing Plant features a state-of-the-art pressure saponification kettle with an 8-bar pressure rating. This advanced system allows the vessel to remain sealed until it reaches 175°C, then vented to evaporate water until the maximum process temperature is achieved. This innovation speeds up the saponification process, significantly increasing the plant’s capacity.
Versatile Batch Production
The pressure saponification kettle is designed with zoned jackets, allowing for smaller batch production if needed. Additionally, the vessel can handle the entire batch without the need for a finishing kettle, providing flexibility for the Grease Manufacturing Plant.
At the heart of the grease manufacturing process lies the Pressure Saponification Kettle, a critical component designed to withstand 8-bar pressure and maintain a sealed environment up to 175°C. This sealed system plays a vital role in accelerating the saponification process by allowing efficient evaporation of water, ensuring that the ideal reaction temperature is reached swiftly.
The jacket zoning system in the kettle allows for flexibility, enabling the production of smaller batches when required. This adaptability ensures that the plant operates efficiently even when full-batch production is not necessary, offering cost-effectiveness and resource optimization.

Finishing Kettles
The finishing section of the Grease Manufacturing Plant includes two 10-tonne atmospheric boiler quality plate carbon steel bodied jacketed kettles. These kettles feature a fully scraped contra-rotating paddle system driven by a pair of stacked gear and motors with concentric shafts, ensuring efficient and consistent mixing.
Once the saponification process is complete, the grease moves to the finishing kettles, where additional processing occurs. These kettles made from boiler-quality carbon steel, each have a 10-tonne capacity and are fitted with a fully scraped, contra-rotating paddle system. This advanced mixing technology, powered by dual-stacked gear motors, ensures that the grease is thoroughly blended, maintaining uniform consistency and texture.
The finishing kettles play a crucial role in modifying the properties of the grease, ensuring that it meets the desired specifications for its intended application.

Charlotte Mill (Grease Manufacturing Plant)
Our Grease Manufacturing Plant is equipped with a Charlotte Mill, mounted on the kettle skid and driven by a 90KW motor. This mill is designed to handle 6800 to 11300 kg/h of grease up to NLGI number 3. The milling gap can be adjusted with a lockable handwheel, providing precise control over the grinding process. After milling, the grease can be re-circulated via the kettle or discharged to packaging or the deaerator.

Advanced Filtration Technology
Our Grease Manufacturing Plant utilizes a high-efficiency filter system, featuring a scraped mesh unit with a wedge wire profile to resist clogging. A pressure difference unit indicates when cleaning is required, and the cleaning system is driven by an electric motor for ease of use.
Efficient Deaeration
The deaerator system in the Grease Manufacturing Plant is an orifice-type in-line unit that agglomerates microscopic air bubbles into larger ones. These larger bubbles burst as the grease is discharged through a nozzle, ensuring a smooth and air-free product.


Cutting-Edge Technology for Grease Manufacturing
Our Grease Manufacturing Plant is built with the latest technology to ensure high-quality grease production. From the pressure saponification kettle to the finishing kettles, Charlotte Mill, and advanced filtration and deaeration systems, every component is designed to maximize efficiency and productivity.
By leveraging these innovative systems and processes, Our Grease Manufacturing Plant is equipped to meet the demands of modern grease production. Our commitment to excellence ensures that every batch of grease produced meets the highest standards of quality and performance.