REGENERATIVE MEDIA BASED POLISHING SYSTEMS

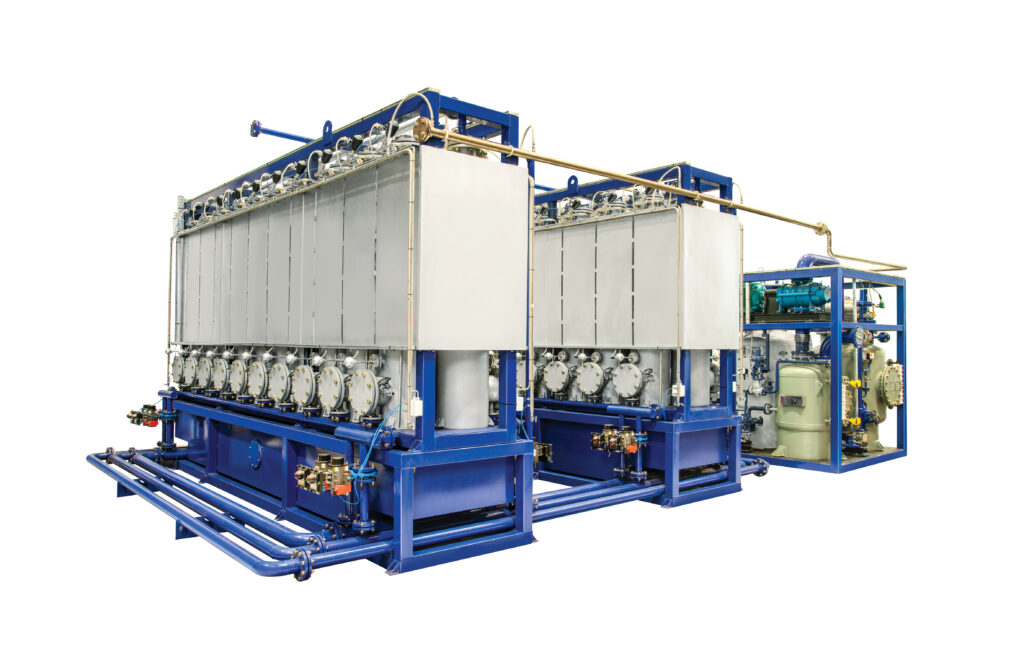
Environmentally Friendly
Regenerative Media Based Polishing Systems
THERMOPAC Polishing System:
- Improves color
- Removes odour
- Reduces sulphur to some extent
- Reduces organic acidity
- Improves oxidation stability
- Has the advantage of higher yields of the finished product when compared with contemporary systems
- Is the only environmental-friendly option to consumable clay and hazardous solvent extraction systems
- Is an economical alternative to potentially hazardous hydrogen treatment plants involving very high pressures and temperatures; and hydrogen plants which are governed by explosive regulations.
- Can be used for parallel or series type of operation.
- Is a modular system.
- Is available for global voltages and frequencies.
The non-consumable polishing system works on the principle of adsorption. The unpolished oil product is passed through this special media several times to get a color close to ASTM A 1 and devoid of odour. Furthermore, it results in reduction of some sulphur. Once the media gets saturated, the media undergoes reactivation at elevated temperature. After the completion of the reactivation process, it is cooled to room temperature and it is ready for reuse. The system comes in two sets of regenerative media based polishing systems; when one set is under reactivation, the other set is in polishing mode. The process loss is only the oil that is burnt during the reactivation process, which is approximately 1% of the weight of the media.
A major advantage of using this special media is that once equilibrium efficiency is obtained, no additional reduction in efficiency occurs with further regenerations.
The highest operating cost is $ 18 per ton of finished product.
The process does not suffer from any of the following drawbacks encountered in the contemporary method of solvent extraction:
- The solvent extraction system needs de-aeration and inert gas blanketing to check deterioration due to oxidation and polymerization.
- It requires azeotropic distillation for solvent purification.
- It should be noted that none of the solvents available is perfectly selective for aromatics.
- Solvent extraction by itself is not a sufficient process; it must be used in combination with other processes.
- One major drawback of solvent extraction is that it removes the unsaturated compounds without conversion, reducing the overall yield.
- It produces API II specification is a false statement because of its inability to remove suphur.
- The health hazards of solvents like NMP need not be over emphasized. The toxic effects of NMP have been documented. When protective measures are not taken, it can cause damage to human organs such as reproductive system, eyes, nose, throat, skin and nervous system.
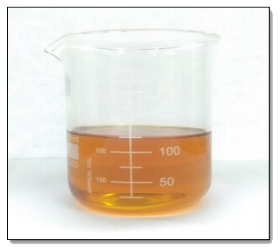
Sr No. | Parameters | Test Method | Unit | HFD |
1 | Appearance | Visual | – | Clear and Bright |
2 | Colour | ASTM –D 1500 | – | <3.0 |
3 | Density at 15 deg C | ASTM -D 1298 | gm/mL | 0.85 – 0.87 |
4 | Kinematic Viscosity at 50 deg C | ASTM -D 445 | cSt | 16- 22 |
5 | Moisture content | ASTM –D 95 | %vol | Nil |
6 | Sulphur Content, max | ASTM -D 4294 | %w/w | 0.3 |
7 | Flash point (PMCC), min | ASTM -D 93 | Deg. C | 100 |
8 | Ash Content | ASTM -D 93 | %w/w | Nil |
9 | Conradson Carbon Residue, max | ASTM -D 189 | %w/w | 0.1 |
10 | Gross Calorific Value | ASTM -D 4868 | kcal/kg | >10000 |
11 | Net Calorific Value | ASTM -D 4868 | kcal/kg | >9000 |